Bossing
Články označené štítkem
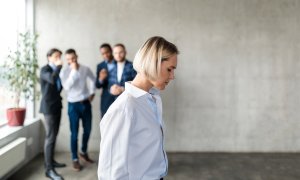
Co dělat, když se setkáte se šikanou na pracovišti
Jsme lidé, máme rozdílné povahy, přístupy, způsob komunikace, zájmy a mnoho dalšího. Hranice mezi legrací a šikanou je často velmi tenká; co je pro jednoho zábava, může být pro jiného ponižující nebo nepříjemné. Z důvodu různosti vzniká prostředí,…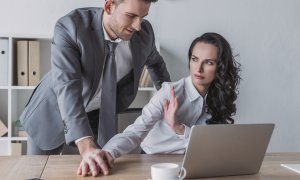